Reducing Carbon Footprints: Decarbonization Approaches for Manufacture of refractory products
This article discusses decarbonization approaches for the manufacture of refractory products, which can help reduce carbon footprints in the industry.
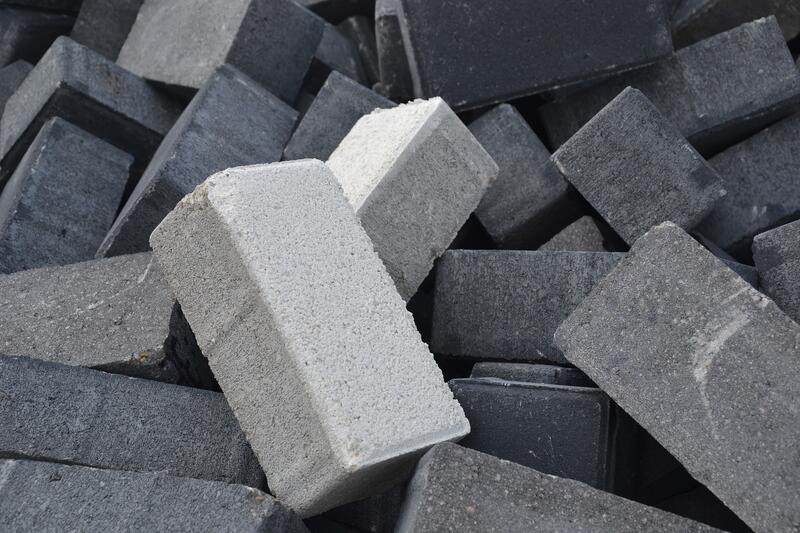
The manufacture of refractory products is an essential industry that provides materials for high-temperature applications in industries such as steel, cement, glass, and ceramics. However, this industry is also a significant contributor to carbon emissions, which exacerbates climate change. Decarbonisation in the manufacture of refractory products sector is, therefore, crucial to mitigate the effects of climate change. This article discusses what decarbonisation is in this sector, the main sources of carbon emissions, how carbon emissions can be reduced, the challenges facing decarbonisation, and the implications of decarbonisation for the industry.
What is Decarbonisation in the Manufacture of Refractory Products Sector and Why is it Important?
Decarbonisation in the manufacture of refractory products sector refers to the process of reducing carbon emissions associated with the production of refractory materials. This involves reducing the use of fossil fuels, increasing energy efficiency, and promoting the use of renewable energy sources. Decarbonisation is important because the manufacture of refractory products is a significant contributor to carbon emissions. According to the International Energy Agency (IEA), the cement, iron, and steel industries account for approximately 20% of global carbon emissions, with refractory production being a significant contributor to these industries.
Moreover, the manufacture of refractory products is an energy-intensive process that requires high temperatures, which are typically generated by burning fossil fuels. This process releases carbon dioxide and other greenhouse gases into the atmosphere, contributing to climate change. Decarbonisation, therefore, is crucial in mitigating the effects of climate change by reducing carbon emissions in the manufacture of refractory products.
Main Sources of Carbon Emissions in the Manufacture of Refractory Products Sector
The main sources of carbon emissions in the manufacture of refractory products sector include the use of fossil fuels, particularly coal, to generate heat in kilns and furnaces. The production of cement, which is a significant consumer of refractory products, is also a significant source of carbon emissions. The production of cement involves the use of limestone, which is heated to high temperatures to produce clinker. This process releases carbon dioxide into the atmosphere, contributing to climate change.
In addition, the production of refractory products involves the use of raw materials that are energy-intensive to extract and process. For instance, the production of alumina, which is a key raw material in the manufacture of refractory products, involves the extraction of bauxite, which requires significant amounts of energy. The transportation of raw materials and finished products also contributes to carbon emissions.
How Can We Reduce Carbon Emissions in the Manufacture of Refractory Products Sector?
There are several ways to reduce carbon emissions in the manufacture of refractory products sector. These include:
1. Switching to Renewable Energy Sources
One way to reduce carbon emissions is to switch to renewable energy sources such as solar, wind, and hydropower. Renewable energy sources are clean and do not emit carbon dioxide or other greenhouse gases. The use of renewable energy sources can, therefore, significantly reduce carbon emissions in the manufacture of refractory products.
2. Improving Energy Efficiency
Improving energy efficiency is another way to reduce carbon emissions. This involves using energy-efficient equipment and processes to reduce the amount of energy required to produce refractory products. For instance, using high-efficiency motors, insulation, and heat recovery systems can significantly reduce energy consumption and carbon emissions.
3. Using Alternative Raw Materials
Using alternative raw materials that require less energy to extract and process can also help reduce carbon emissions. For instance, using recycled materials such as scrap metal and waste refractory materials can reduce the energy required to produce new refractory products.
4. Carbon Capture and Storage
Carbon capture and storage (CCS) involves capturing carbon dioxide emissions from industrial processes and storing them underground. CCS can significantly reduce carbon emissions in the manufacture of refractory products.
5. Process Optimization
Optimizing production processes can also help reduce carbon emissions. This involves identifying and eliminating inefficiencies in the production process to reduce energy consumption and carbon emissions.
Challenges Facing Decarbonisation in the Manufacture of Refractory Products Sector
Despite the benefits of decarbonisation, several challenges hinder its implementation in the manufacture of refractory products sector. These include:
1. High Costs
Decarbonisation requires significant investments in new technologies and equipment, which can be costly. The high costs of decarbonisation can make it challenging for companies to adopt new technologies and processes.
2. Lack of Incentives
The lack of incentives for companies to reduce carbon emissions can also hinder decarbonisation. In some cases, companies may not see the benefits of reducing carbon emissions or may not be motivated to do so.
3. Technical Challenges
Decarbonisation in the manufacture of refractory products sector also faces technical challenges. For instance, the use of renewable energy sources may not be feasible in some locations due to factors such as weather patterns and land availability. Similarly, the use of alternative raw materials may not be possible in some cases due to technical limitations.
4. Lack of Regulations
The lack of regulations or weak regulations can also hinder decarbonisation. In some countries, there may be no regulations or weak regulations that do not require companies to reduce carbon emissions. This can make it challenging for companies to invest in decarbonisation.
Implications of Decarbonisation for the Manufacture of Refractory Products Sector
Decarbonisation has several implications for the manufacture of refractory products sector. These include:
1. Increased Competitiveness
Companies that adopt decarbonisation strategies can become more competitive by reducing their costs and improving their environmental performance. This can help companies attract customers who are increasingly concerned about the environmental impact of the products they buy.
2. Improved Environmental Performance
Decarbonisation can significantly reduce the environmental impact of the manufacture of refractory products. By reducing carbon emissions, decarbonisation can help mitigate the effects of climate change and reduce air pollution.
3. Innovation Opportunities
Decarbonisation can also create opportunities for innovation and new business models. For instance, the use of renewable energy sources can create opportunities for companies to develop new technologies and processes that can be used in other industries.
Conclusion
Decarbonisation in the manufacture of refractory products sector is crucial in mitigating the effects of climate change. The main sources of carbon emissions in this sector include the use of fossil fuels, the production of cement, and the extraction and processing of raw materials. To reduce carbon emissions, companies can switch to renewable energy sources, improve energy efficiency, use alternative raw materials, adopt carbon capture and storage, and optimize production processes. However, decarbonisation faces several challenges, including high costs, lack of incentives, technical challenges, and weak regulations. Decarbonisation has several implications for the industry, including increased competitiveness, improved environmental performance, and innovation opportunities.