Decarbonization in Manufacture of electric lighting equipment: Strategies for a Greener Future
This article discusses strategies for reducing carbon emissions in the manufacture of electric lighting equipment, highlighting the importance of decarbonization for a greener future.
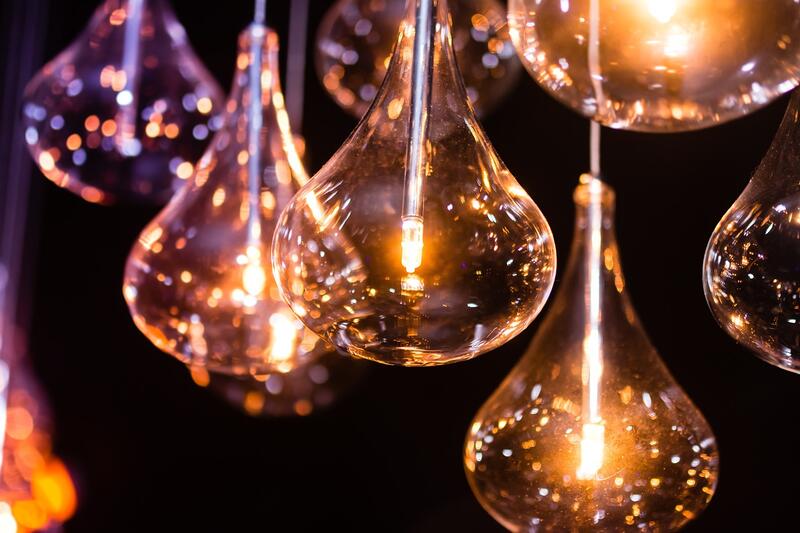
The manufacture of electric lighting equipment is a vital industry that has been growing rapidly in recent years. However, this growth has come at a cost, as the sector has been identified as a major contributor to global carbon emissions. In response, there has been a growing push towards decarbonisation in the industry, with companies and governments alike seeking to reduce their carbon footprint. In this article, we will explore what decarbonisation means in the context of the manufacture of electric lighting equipment, why it is important, the main sources of carbon emissions in the sector, how we can reduce these emissions, the challenges facing decarbonisation, and the implications of decarbonisation for the industry.
What is Decarbonisation in the Manufacture of Electric Lighting Equipment Sector and Why is it Important?
Decarbonisation refers to the process of reducing the amount of carbon emissions produced by a particular industry or sector. In the context of the manufacture of electric lighting equipment, decarbonisation involves reducing the carbon footprint of the industry by reducing the emissions produced during the manufacturing process. This is important because the manufacture of electric lighting equipment is a significant contributor to global carbon emissions, and reducing these emissions is essential if we are to mitigate the effects of climate change.
The Main Sources of Carbon Emissions in the Manufacture of Electric Lighting Equipment Sector
The manufacture of electric lighting equipment involves a range of processes, each of which contributes to carbon emissions in different ways. The main sources of carbon emissions in the sector include:
- Energy Use: The manufacture of electric lighting equipment requires a significant amount of energy, which is typically generated from fossil fuels. This energy is used to power the machinery and equipment used in the manufacturing process, as well as to heat and cool the manufacturing facilities.
- Raw Materials: The production of electric lighting equipment requires a range of raw materials, including metals, plastics, and glass. The extraction and processing of these materials can be energy-intensive and can produce significant carbon emissions.
- Transportation: The transportation of raw materials and finished products to and from manufacturing facilities can also contribute to carbon emissions. This is particularly true for products that are manufactured in one part of the world and then shipped to another part of the world for distribution.
How Can We Reduce Carbon Emissions in the Manufacture of Electric Lighting Equipment Sector?
Reducing carbon emissions in the manufacture of electric lighting equipment sector requires a range of strategies, including:
- Energy Efficiency: One of the most effective ways to reduce carbon emissions in the sector is to improve energy efficiency. This can be achieved by upgrading machinery and equipment to more energy-efficient models, implementing energy-saving measures in manufacturing facilities, and using renewable energy sources such as solar and wind power.
- Sustainable Materials: The use of sustainable materials in the manufacture of electric lighting equipment can also help to reduce carbon emissions. This includes using recycled materials where possible, sourcing materials from sustainable sources, and reducing the amount of material used in the manufacturing process.
- Transportation: Reducing the carbon footprint of transportation is another key strategy for reducing carbon emissions in the sector. This can be achieved by using more efficient modes of transportation such as rail and sea freight, and by reducing the distance that products need to travel.
What are the Challenges Facing Decarbonisation in the Manufacture of Electric Lighting Equipment Sector?
Despite the many benefits of decarbonisation, there are also a range of challenges facing the sector. These include:
- Cost: Decarbonisation can be expensive, particularly for smaller companies that may not have the resources to invest in new equipment or technologies.
- Resistance to Change: Some companies may be resistant to change, particularly if they have been operating in a certain way for many years. This can make it difficult to implement new strategies for reducing carbon emissions.
- Lack of Regulation: In some countries, there may be a lack of regulation around carbon emissions, which can make it difficult for companies to justify the cost of decarbonisation.
What are the Implications of Decarbonisation for the Manufacture of Electric Lighting Equipment Sector?
Decarbonisation has a range of implications for the manufacture of electric lighting equipment sector, including:
- Increased Competition: Companies that are able to reduce their carbon footprint may have a competitive advantage over those that do not, particularly as consumers become more environmentally conscious.
- Innovation: Decarbonisation is driving innovation in the sector, with companies developing new technologies and processes to reduce carbon emissions.
- Reputation: Companies that are seen to be taking action to reduce their carbon footprint may benefit from a positive reputation, which can help to attract customers and investors.
Conclusion
Decarbonisation is essential if we are to mitigate the effects of climate change, and the manufacture of electric lighting equipment sector has an important role to play in this process. By reducing carbon emissions through energy efficiency, sustainable materials, and transportation, the sector can help to reduce its impact on the environment. While there are challenges to decarbonisation, the benefits are clear, including increased competition, innovation, and a positive reputation. As such, it is essential that companies and governments continue to invest in decarbonisation strategies to ensure a sustainable future for the industry and the planet.