Strategies to Achieve Decarbonization in Manufacture of cement, lime and plaster
This article discusses various strategies and technologies that can be implemented to achieve decarbonization in the manufacturing processes of cement, lime, and plaster.
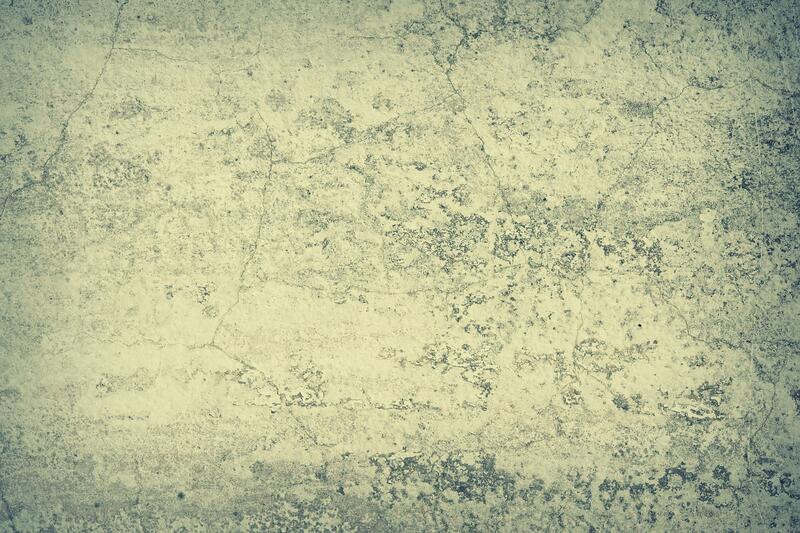
What is Decarbonisation in "Manufacture of Cement, Lime and Plaster" Sector and Why is it Important?
Decarbonisation refers to the process of reducing or eliminating carbon emissions in various sectors of the economy. In the context of the manufacture of cement, lime, and plaster, decarbonisation involves reducing the carbon footprint of the sector by adopting cleaner production methods, reducing energy consumption, and using alternative fuels. The importance of decarbonisation in this sector cannot be overstated. The manufacture of cement, lime, and plaster is energy-intensive, and the production process emits significant amounts of carbon dioxide. The sector is, therefore, a significant contributor to greenhouse gas emissions, which are responsible for climate change. Decarbonisation is, therefore, crucial in mitigating the adverse effects of climate change.
What are the Main Sources of Carbon Emissions in "Manufacture of Cement, Lime and Plaster" Sector?
The manufacture of cement, lime, and plaster is an energy-intensive process that involves the use of fossil fuels. The main sources of carbon emissions in this sector include:
- Energy Consumption: The production process requires a lot of energy, which is mainly derived from fossil fuels such as coal, oil, and gas. The combustion of these fuels emits significant amounts of carbon dioxide.
- Raw Materials: The production of cement, lime, and plaster requires raw materials such as limestone, clay, and gypsum. The extraction and transportation of these raw materials also contribute to carbon emissions.
- Chemical Reactions: The production process involves chemical reactions that release carbon dioxide. For example, the calcination of limestone during the production of cement releases carbon dioxide.
- Transportation: The transportation of raw materials and finished products also contributes to carbon emissions. The use of fossil fuels in transportation emits carbon dioxide.
How Can We Reduce Carbon Emissions in "Manufacture of Cement, Lime and Plaster" Sector?
Reducing carbon emissions in the manufacture of cement, lime, and plaster sector requires a combination of measures, including:
- Use of Alternative Fuels: The use of alternative fuels such as biomass, waste, and renewable energy sources such as solar and wind can significantly reduce carbon emissions. Alternative fuels can replace fossil fuels, reducing the carbon footprint of the sector.
- Energy Efficiency: Improving energy efficiency in the production process can significantly reduce carbon emissions. This can be achieved through the use of energy-efficient equipment, process optimization, and waste heat recovery.
- Carbon Capture and Storage: Carbon capture and storage (CCS) involves capturing carbon dioxide emissions from the production process and storing them underground. CCS can significantly reduce carbon emissions in the sector.
- Material Efficiency: Improving material efficiency in the production process can reduce the amount of raw materials required, reducing carbon emissions associated with their extraction and transportation.
- Product Innovation: Developing innovative products that require less energy to produce can significantly reduce carbon emissions in the sector.
What are the Challenges Facing Decarbonisation in "Manufacture of Cement, Lime and Plaster" Sector?
Decarbonisation in the manufacture of cement, lime, and plaster sector faces several challenges, including:
- High Capital Costs: The adoption of cleaner production methods and technologies requires significant capital investments, which may be a challenge for smaller companies.
- Lack of Incentives: The lack of incentives for companies to reduce their carbon footprint may hinder decarbonisation efforts.
- Technological Limitations: The development of new technologies that can significantly reduce carbon emissions in the sector is still in its early stages, and there are limitations to current technologies.
- Regulatory Framework: The lack of a robust regulatory framework to encourage decarbonisation in the sector may hinder progress.
What are the Implications of Decarbonisation for "Manufacture of Cement, Lime and Plaster" Sector?
Decarbonisation in the manufacture of cement, lime, and plaster sector has several implications, including:
- Reduced Carbon Footprint: Decarbonisation efforts will significantly reduce the carbon footprint of the sector, contributing to global efforts to mitigate climate change.
- Increased Competitiveness: Companies that adopt cleaner production methods and technologies will be more competitive in a low-carbon economy.
- New Opportunities: Decarbonisation efforts will create new opportunities for companies that develop innovative products and technologies that reduce carbon emissions.
- Regulatory Compliance: Companies will need to comply with new regulations aimed at reducing carbon emissions, which may require significant investments in cleaner production methods and technologies.
Conclusion
Decarbonisation in the manufacture of cement, lime, and plaster sector is crucial in mitigating the adverse effects of climate change. The sector is a significant contributor to carbon emissions globally, and reducing its carbon footprint requires a combination of measures, including the use of alternative fuels, energy efficiency, carbon capture and storage, material efficiency, and product innovation. Decarbonisation efforts face several challenges, including high capital costs, lack of incentives, technological limitations, and regulatory frameworks. The implications of decarbonisation for the sector include reduced carbon footprint, increased competitiveness, new opportunities, and regulatory compliance. The sector must embrace decarbonisation to contribute to global efforts to mitigate climate change.