Charting the Course to Decarbonization in Manufacture of refractory products: Strategies and Initiatives
This article highlights strategies and initiatives for decarbonization in the manufacturing of refractory products, which are essential for numerous industries including steel and cement production.
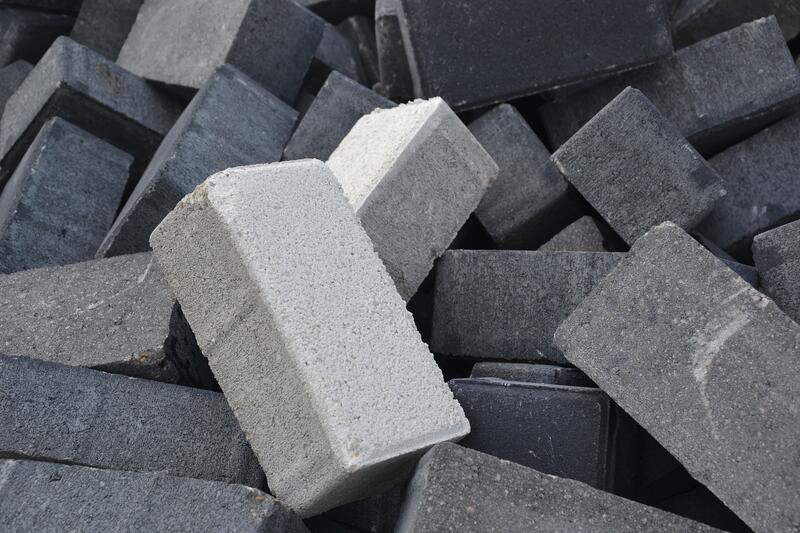
Introduction
The manufacturing sector is one of the largest contributors to global carbon emissions, accounting for about 25% of the total. The manufacture of refractory products, which are essential materials for high-temperature industrial processes, is no exception. Refractory products are used in various industries such as steel, cement, glass, petrochemicals, and ceramics. The production of these products involves energy-intensive processes that emit significant amounts of greenhouse gases (GHGs), mainly carbon dioxide (CO2). Therefore, decarbonisation of the manufacture of refractory products is crucial for achieving global climate goals and reducing the carbon footprint of industrial processes. This article will discuss the importance of decarbonisation in the manufacture of refractory products sector, the main sources of carbon emissions, reduction strategies, challenges, and implications.
What is Decarbonisation in the Manufacture of Refractory Products Sector and Why is it Important?
Decarbonisation is the process of reducing or eliminating carbon emissions from industrial processes, transportation, and energy production. In the manufacture of refractory products sector, decarbonisation involves reducing the carbon footprint of the production processes and the products themselves. The importance of decarbonisation in this sector is twofold. First, refractory products are essential materials for high-temperature industrial processes that emit significant amounts of GHGs. Therefore, reducing the carbon footprint of these products can contribute to the reduction of GHG emissions from various industries. Second, the manufacture of refractory products is a significant contributor to global carbon emissions. Therefore, decarbonisation of this sector can contribute to achieving global climate goals and reducing the carbon footprint of the manufacturing sector.
Main Sources of Carbon Emissions in the Manufacture of Refractory Products Sector
The manufacture of refractory products involves energy-intensive processes that emit significant amounts of GHGs. The main sources of carbon emissions in this sector are:
- Energy Consumption: The production of refractory products requires high-temperature processes that consume large amounts of energy. The energy is mainly derived from fossil fuels such as coal, oil, and natural gas, which emit significant amounts of CO2.
- Raw Materials: The raw materials used in the production of refractory products, such as clay, silica, and alumina, are often mined, transported, and processed using energy-intensive methods that emit GHGs.
- Manufacturing Processes: The manufacturing processes of refractory products, such as drying, firing, and sintering, emit significant amounts of GHGs, mainly CO2, due to the combustion of fossil fuels.
- Waste Management: The disposal of waste materials generated during the production of refractory products, such as spent refractory bricks, also contributes to carbon emissions.
Reduction Strategies for Carbon Emissions in the Manufacture of Refractory Products Sector
Reducing carbon emissions in the manufacture of refractory products sector requires a combination of strategies that target the main sources of emissions. The following are some of the reduction strategies that can be implemented:
- Energy Efficiency: Improving energy efficiency in the production processes can reduce the amount of energy consumed and, therefore, the amount of carbon emissions. This can be achieved through the use of energy-efficient equipment, process optimization, and waste heat recovery.
- Renewable Energy: Switching to renewable energy sources such as solar, wind, and geothermal can significantly reduce carbon emissions in the manufacture of refractory products sector. This can be achieved through the installation of renewable energy systems on-site or sourcing renewable energy from off-site.
- Raw Material Efficiency: Reducing the amount of raw materials used in the production processes can reduce the amount of energy required and, therefore, the amount of carbon emissions. This can be achieved through the use of recycled materials, process optimization, and waste reduction.
- Carbon Capture and Storage (CCS): CCS is a technology that captures carbon emissions from industrial processes and stores them underground. This technology can be applied to the manufacture of refractory products sector to capture and store carbon emissions from the production processes.
Challenges Facing Decarbonisation in the Manufacture of Refractory Products Sector
Decarbonisation of the manufacture of refractory products sector faces several challenges, including:
- Cost: Implementing decarbonisation strategies can be expensive, and the cost may be passed on to consumers, making the products less competitive in the market.
- Technical Feasibility: Some decarbonisation strategies, such as CCS, may not be technically feasible for some refractory product manufacturing processes.
- Regulatory Framework: The lack of a regulatory framework that incentivizes decarbonisation can hinder the adoption of decarbonisation strategies.
- Supply Chain Complexity: The supply chain for raw materials used in the manufacture of refractory products is complex and may involve multiple suppliers, making it difficult to track the carbon footprint of the products.
Implications of Decarbonisation for the Manufacture of Refractory Products Sector
Decarbonisation of the manufacture of refractory products sector has several implications, including:
- Market Competitiveness: Decarbonisation can increase the market competitiveness of refractory products by reducing their carbon footprint and meeting the growing demand for sustainable products.
- Innovation: Decarbonisation can drive innovation in the manufacture of refractory products sector by encouraging the development of new materials and processes that have a lower carbon footprint.
- Regulation: Decarbonisation can lead to the introduction of regulations that incentivize the adoption of decarbonisation strategies and penalize high carbon-emitting products.
- Collaboration: Decarbonisation can encourage collaboration between manufacturers, suppliers, and customers to reduce the carbon footprint of the supply chain.
Conclusion
Decarbonisation of the manufacture of refractory products sector is crucial for achieving global climate goals and reducing the carbon footprint of industrial processes. The main sources of carbon emissions in this sector are energy consumption, raw materials, manufacturing processes, and waste management. Reduction strategies for carbon emissions in this sector include energy efficiency, renewable energy, raw material efficiency, and CCS. However, decarbonisation faces several challenges, including cost, technical feasibility, regulatory framework, and supply chain complexity. Decarbonisation has several implications, including market competitiveness, innovation, regulation, and collaboration. Therefore, decarbonisation of the manufacture of refractory products sector requires a combination of strategies, collaboration, and regulatory frameworks that incentivize the adoption of decarbonisation strategies.