Sustainable Transitions: Decarbonizing Manufacture of fibre cement Strategies
This article discusses strategies for reducing carbon emissions in the production of fiber cement, a commonly used building material, to support sustainable transitions.
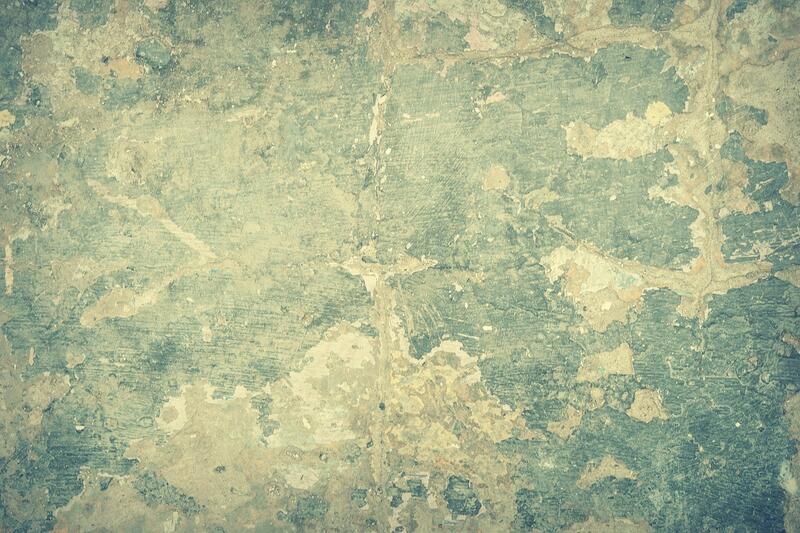
The manufacture of fibre cement is an important industry that produces a wide range of products, including roofing sheets, wall cladding, pipes, and other building materials. However, like many other industries, the manufacture of fibre cement is a significant contributor to greenhouse gas emissions, particularly carbon dioxide (CO2). Decarbonisation is the process of reducing or eliminating carbon emissions from industrial processes, and it is crucial for the sustainability of the manufacturing sector. This article will explore the concept of decarbonisation in the manufacture of fibre cement sector, its importance, the main sources of carbon emissions, strategies for reducing carbon emissions, challenges facing decarbonisation, and the implications of decarbonisation for the industry.
What is Decarbonisation in the Manufacture of Fibre Cement Sector, and Why is it Important?
Decarbonisation is the process of reducing or eliminating carbon emissions from industrial processes. In the manufacture of fibre cement, decarbonisation involves reducing the carbon footprint of the production process, from the extraction of raw materials to the final product. The importance of decarbonisation in the manufacture of fibre cement sector cannot be overstated. The industry is a significant contributor to greenhouse gas emissions, particularly carbon dioxide (CO2), which is a major driver of climate change. According to the International Energy Agency (IEA), the cement industry alone is responsible for around 7% of global CO2 emissions. Therefore, decarbonisation is essential to mitigate the impact of climate change and achieve global climate goals.
Main Sources of Carbon Emissions in the Manufacture of Fibre Cement Sector
The manufacture of fibre cement involves several processes that contribute to carbon emissions. The main sources of carbon emissions in the manufacture of fibre cement sector include:
- Raw material extraction: The extraction of raw materials such as limestone and clay involves the use of heavy machinery and transportation, which consume fossil fuels and emit carbon dioxide.
- Energy consumption: The production process of fibre cement requires a significant amount of energy, mainly in the form of electricity and heat. The energy is typically generated from fossil fuels such as coal and natural gas, which emit carbon dioxide.
- Chemical reactions: The production process of fibre cement involves chemical reactions that release carbon dioxide. For instance, the calcination of limestone to produce cement releases carbon dioxide.
- Transportation: The transportation of raw materials and finished products to and from the manufacturing site also contributes to carbon emissions.
Strategies for Reducing Carbon Emissions in the Manufacture of Fibre Cement Sector
Decarbonisation in the manufacture of fibre cement sector requires a comprehensive approach that addresses the entire production process. Here are some strategies for reducing carbon emissions in the industry:
- Use of alternative raw materials: The use of alternative raw materials such as industrial waste, recycled materials, and biomass can reduce the carbon footprint of the production process. For instance, the use of fly ash from coal-fired power plants as a substitute for cement can reduce carbon emissions.
- Energy efficiency: Improving energy efficiency in the production process can significantly reduce carbon emissions. This can be achieved through the use of energy-efficient equipment, optimization of production processes, and the use of renewable energy sources such as solar and wind.
- Carbon capture and storage (CCS): CCS involves capturing carbon dioxide emissions from industrial processes and storing them underground. This technology can significantly reduce carbon emissions in the manufacture of fibre cement sector.
- Process optimization: Optimizing the production process can reduce the amount of energy and raw materials required, thus reducing carbon emissions. For instance, the use of advanced kiln technology can reduce the amount of energy required to produce cement.
- Circular economy: Adopting a circular economy approach can reduce the carbon footprint of the production process. This involves reducing waste, reusing materials, and recycling products.
Challenges Facing Decarbonisation in the Manufacture of Fibre Cement Sector
Despite the importance of decarbonisation in the manufacture of fibre cement sector, several challenges hinder its implementation. Here are some of the challenges:
- Cost: Decarbonisation strategies such as energy efficiency, CCS, and the use of alternative raw materials require significant investment, which may be a challenge for some manufacturers.
- Technological barriers: Some decarbonisation technologies such as CCS and advanced kiln technology are still in the development stage and may not be readily available or affordable for some manufacturers.
- Regulatory barriers: The lack of supportive policies and regulations can hinder the adoption of decarbonisation strategies. For instance, the absence of carbon pricing mechanisms may discourage manufacturers from investing in decarbonisation.
- Lack of awareness: Some manufacturers may not be aware of the benefits of decarbonisation or may not have the necessary knowledge and skills to implement decarbonisation strategies.
Implications of Decarbonisation for the Manufacture of Fibre Cement Sector
Decarbonisation has several implications for the manufacture of fibre cement sector. Here are some of the implications:
- Increased competitiveness: Decarbonisation can improve the competitiveness of manufacturers by reducing their carbon footprint and enhancing their reputation as environmentally responsible companies.
- Reduced costs: Decarbonisation strategies such as energy efficiency and the use of alternative raw materials can reduce the cost of production, thus improving the profitability of manufacturers.
- Improved environmental performance: Decarbonisation can significantly reduce the carbon footprint of the manufacture of fibre cement sector, thus contributing to the global effort to mitigate climate change.
- Increased innovation: Decarbonisation requires the development of new technologies and processes, which can drive innovation and create new business opportunities.
Conclusion
Decarbonisation is essential for the sustainability of the manufacture of fibre cement sector. The industry is a significant contributor to greenhouse gas emissions, particularly carbon dioxide, which is a major driver of climate change. Decarbonisation strategies such as the use of alternative raw materials, energy efficiency, CCS, process optimization, and circular economy can significantly reduce carbon emissions in the industry. However, several challenges such as cost, technological barriers, regulatory barriers, and lack of awareness hinder the implementation of decarbonisation strategies. The implications of decarbonisation for the manufacture of fibre cement sector include increased competitiveness, reduced costs, improved environmental performance, and increased innovation. Therefore, stakeholders in the industry should collaborate to overcome the challenges and implement decarbonisation strategies to achieve a sustainable future.