Navigating the Path to Decarbonization in Manufacture of ceramic insulators and insulating fittings
This article discusses the challenges and opportunities faced by the ceramic insulator and insulating fittings manufacturing industry in their journey towards decarbonization.
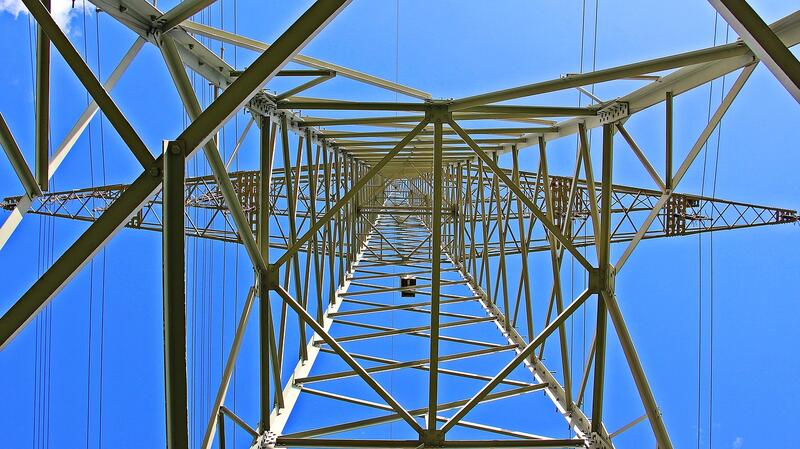
The manufacture of ceramic insulators and insulating fittings is an essential part of the energy sector. These products are used in power transmission and distribution systems to insulate and protect electrical equipment from high voltage and current. However, the production of ceramic insulators and insulating fittings is a carbon-intensive process that contributes to climate change. Decarbonisation is the process of reducing carbon emissions to mitigate climate change. In this article, we will explore the importance of decarbonisation in the manufacture of ceramic insulators and insulating fittings sector, the main sources of carbon emissions, ways to reduce carbon emissions, challenges facing decarbonisation, and the implications of decarbonisation for the sector.
What is Decarbonisation in "Manufacture of Ceramic Insulators and Insulating Fittings" Sector and Why is it Important?
Decarbonisation is the process of reducing carbon emissions to mitigate climate change. The manufacture of ceramic insulators and insulating fittings is a carbon-intensive process that contributes to climate change. The sector is responsible for a significant amount of greenhouse gas emissions, including carbon dioxide (CO2), methane (CH4), and nitrous oxide (N2O). These emissions are released during the production of raw materials, energy consumption, and transportation of finished products. Decarbonisation is important for the sector because it can help reduce the environmental impact of the industry and mitigate climate change.
The Main Sources of Carbon Emissions in "Manufacture of Ceramic Insulators and Insulating Fittings" Sector
The main sources of carbon emissions in the manufacture of ceramic insulators and insulating fittings sector include:
- Raw materials: The production of raw materials such as clay, feldspar, and quartz requires energy and releases carbon emissions.
- Energy consumption: The firing process in the production of ceramic insulators and insulating fittings requires high temperatures, which are achieved through the use of fossil fuels such as natural gas and coal.
- Transportation: The transportation of raw materials and finished products also contributes to carbon emissions.
How Can We Reduce Carbon Emissions in "Manufacture of Ceramic Insulators and Insulating Fittings" Sector?
There are several ways to reduce carbon emissions in the manufacture of ceramic insulators and insulating fittings sector, including:
- Use of renewable energy sources: The use of renewable energy sources such as solar, wind, and hydroelectric power can reduce carbon emissions from energy consumption.
- Energy efficiency: Improving energy efficiency in the manufacturing process can reduce energy consumption and carbon emissions.
- Recycling and waste reduction: Recycling and waste reduction can reduce the need for raw materials and energy consumption, thereby reducing carbon emissions.
- Carbon capture and storage: Carbon capture and storage (CCS) is a technology that captures carbon emissions from industrial processes and stores them underground.
- Sustainable transportation: The use of sustainable transportation such as electric vehicles and public transportation can reduce carbon emissions from transportation.
What are the Challenges Facing Decarbonisation in "Manufacture of Ceramic Insulators and Insulating Fittings" Sector?
There are several challenges facing decarbonisation in the manufacture of ceramic insulators and insulating fittings sector, including:
- Cost: The implementation of decarbonisation measures can be expensive, and the cost may be passed on to consumers.
- Technical challenges: The implementation of decarbonisation measures may require changes to manufacturing processes, which can be technically challenging.
- Lack of incentives: There may be a lack of incentives for companies to invest in decarbonisation measures.
- Regulatory challenges: Regulations may not be in place to encourage or require companies to reduce carbon emissions.
- Supply chain challenges: The supply chain for raw materials and transportation may not be set up to support decarbonisation measures.
What are the Implications of Decarbonisation for "Manufacture of Ceramic Insulators and Insulating Fittings" Sector?
Decarbonisation has several implications for the manufacture of ceramic insulators and insulating fittings sector, including:
- Increased competition: Companies that invest in decarbonisation measures may have a competitive advantage over those that do not.
- Innovation: The implementation of decarbonisation measures may require innovation in manufacturing processes and technologies.
- Consumer demand: Consumers may prefer products that are produced with decarbonisation measures, which could drive demand for sustainable products.
- Regulatory compliance: Regulations may require companies to reduce carbon emissions, which could lead to the implementation of decarbonisation measures.
Conclusion
The manufacture of ceramic insulators and insulating fittings is a carbon-intensive process that contributes to climate change. Decarbonisation is the process of reducing carbon emissions to mitigate climate change. The sector can reduce carbon emissions through the use of renewable energy sources, energy efficiency, recycling and waste reduction, carbon capture and storage, and sustainable transportation. However, there are several challenges facing decarbonisation, including cost, technical challenges, lack of incentives, regulatory challenges, and supply chain challenges. Decarbonisation has several implications for the sector, including increased competition, innovation, consumer demand, and regulatory compliance. The implementation of decarbonisation measures is essential to reduce the environmental impact of the industry and mitigate climate change.