Innovative Solutions for Decarbonizing Manufacture of basic metals
This article explores new and innovative approaches to reduce the carbon footprint in the manufacturing of basic metals, including steel and aluminum.
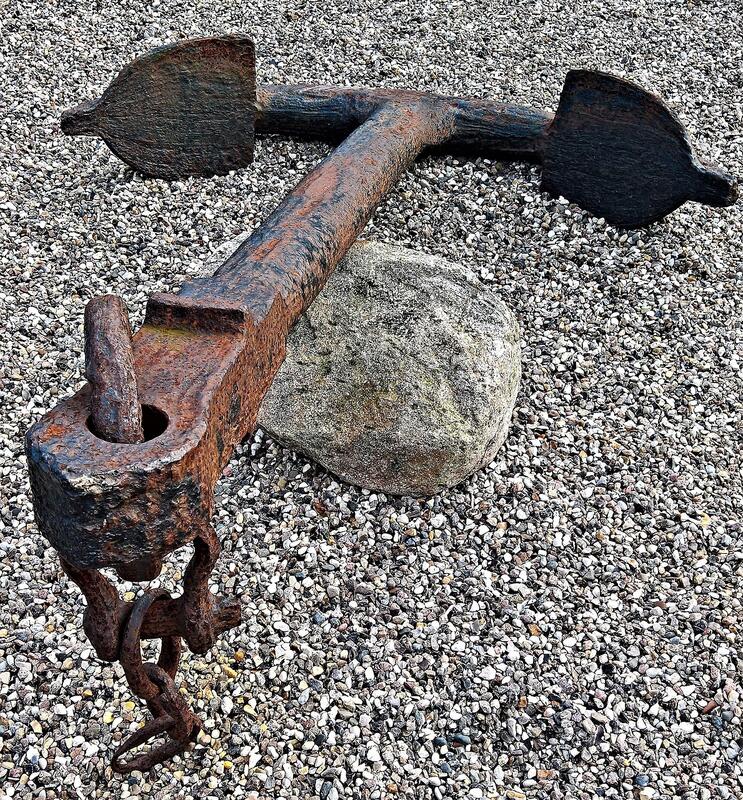
Introduction
The manufacture of basic metals is a critical sector that supports various industries, such as construction, automotive, electronics, and energy. However, this sector is also a significant contributor to greenhouse gas (GHG) emissions, particularly carbon dioxide (CO2), which is a primary driver of climate change. As such, decarbonisation of the manufacture of basic metals sector is essential to mitigate the adverse effects of climate change and achieve the global goal of limiting the temperature rise to below 2°C above pre-industrial levels. This article explores the concept of decarbonisation in the manufacture of basic metals sector, its importance, sources of carbon emissions, reduction strategies, challenges, and implications.
What is Decarbonisation in the Manufacture of Basic Metals Sector and Why is it Important?
Decarbonisation in the manufacture of basic metals sector refers to the process of reducing or eliminating carbon emissions associated with the production of metals, such as iron, steel, aluminum, and copper, among others. This process involves adopting cleaner and more efficient technologies, using renewable energy sources, improving energy efficiency, and promoting circular economy principles, among other measures. Decarbonisation is important for several reasons, including:
- Climate Change Mitigation: The manufacture of basic metals sector is responsible for about 7% of global GHG emissions, primarily from the use of fossil fuels in the production process. Decarbonisation is crucial to reduce these emissions and mitigate the adverse effects of climate change, such as extreme weather events, sea-level rise, and biodiversity loss.
- Energy Security: Decarbonisation can enhance energy security by reducing dependence on fossil fuels, which are finite and subject to price volatility and geopolitical risks. By using renewable energy sources, such as solar, wind, and hydropower, the manufacture of basic metals sector can ensure a more stable and affordable energy supply.
- Competitiveness: Decarbonisation can improve the competitiveness of the manufacture of basic metals sector by reducing production costs, enhancing resource efficiency, and meeting the growing demand for sustainable products. This can also create new business opportunities and jobs in the green economy.
What are the Main Sources of Carbon Emissions in the Manufacture of Basic Metals Sector?
The manufacture of basic metals sector emits carbon dioxide (CO2) from various sources, including:
- Energy Use: The production of basic metals requires significant amounts of energy, which is mostly derived from fossil fuels, such as coal, oil, and natural gas. The combustion of these fuels releases CO2 into the atmosphere, contributing to climate change.
- Raw Materials: The extraction and processing of raw materials, such as iron ore, bauxite, and copper, also emit CO2. For instance, the production of iron and steel involves the reduction of iron ore using carbon-based fuels, which releases CO2 as a by-product.
- Transportation: The transportation of raw materials, products, and waste generates CO2 emissions, particularly from the use of diesel-powered trucks, ships, and trains.
- Waste Management: The disposal of waste, such as slag, dust, and emissions control residues, also contributes to CO2 emissions, particularly from the incineration of hazardous waste.
How Can We Reduce Carbon Emissions in the Manufacture of Basic Metals Sector?
To reduce carbon emissions in the manufacture of basic metals sector, various strategies can be adopted, including:
- Energy Efficiency: Improving energy efficiency can reduce the amount of energy required to produce basic metals, thereby reducing carbon emissions. This can be achieved through measures such as process optimization, heat recovery, and the use of energy-efficient equipment.
- Renewable Energy: Using renewable energy sources, such as solar, wind, and hydropower, can reduce the reliance on fossil fuels and lower carbon emissions. This can be achieved through on-site renewable energy generation, such as solar panels and wind turbines, or sourcing renewable energy from the grid.
- Carbon Capture, Utilization, and Storage (CCUS): CCUS involves capturing carbon emissions from the production process, converting them into useful products, such as chemicals and fuels, and storing them underground or in other long-term storage facilities. CCUS can significantly reduce carbon emissions in the manufacture of basic metals sector, particularly in steel production.
- Circular Economy: The circular economy approach involves reducing waste and maximizing the value of resources by reusing, recycling, and recovering materials and energy. This can reduce the need for virgin raw materials and lower carbon emissions.
What are the Challenges Facing Decarbonisation in the Manufacture of Basic Metals Sector?
Despite the potential benefits of decarbonisation in the manufacture of basic metals sector, several challenges exist, including:
- High Capital Costs: Many decarbonisation technologies, such as CCUS and renewable energy, require significant upfront investment, which may be a barrier for some companies, particularly small and medium-sized enterprises (SMEs).
- Technical Feasibility: Some decarbonisation technologies, such as CCUS, are still in the early stages of development and may not be technically feasible or cost-effective for some applications.
- Regulatory Uncertainty: The lack of clear and consistent policies and regulations to support decarbonisation can create uncertainty and discourage investment in clean technologies.
- Supply Chain Complexity: The manufacture of basic metals sector involves complex supply chains, with multiple stakeholders and diverse environmental and social impacts. Decarbonisation requires collaboration and coordination among these stakeholders, which can be challenging.
What are the Implications of Decarbonisation for the Manufacture of Basic Metals Sector?
Decarbonisation can have several implications for the manufacture of basic metals sector, including:
- Innovation and Investment: Decarbonisation can spur innovation and investment in clean technologies, such as renewable energy, CCUS, and circular economy, which can create new business opportunities and jobs.
- Competitiveness and Market Access: Decarbonisation can enhance the competitiveness of the manufacture of basic metals sector by improving resource efficiency, reducing costs, and meeting the growing demand for sustainable products. It can also provide access to new markets, such as those that require low-carbon products.
- Collaboration and Coordination: Decarbonisation requires collaboration and coordination among stakeholders, including governments, industry, academia, and civil society. This can foster partnerships and dialogue to address common challenges and opportunities.
- Environmental and Social Benefits: Decarbonisation can deliver environmental and social benefits, such as reduced air pollution, improved health, and enhanced social equity. It can also contribute to the achievement of the Sustainable Development Goals (SDGs), particularly SDG 7 (Affordable and Clean Energy) and SDG 13 (Climate Action).
Conclusion
Decarbonisation of the manufacture of basic metals sector is essential to mitigate the adverse effects of climate change and achieve the global goal of limiting the temperature rise to below 2°C above pre-industrial levels. This requires adopting cleaner and more efficient technologies, using renewable energy sources, improving energy efficiency, and promoting circular economy principles, among other measures. However, several challenges exist, including high capital costs, technical feasibility, regulatory uncertainty, and supply chain complexity. Decarbonisation can have several implications for the manufacture of basic metals sector, including innovation and investment, competitiveness and market access, collaboration and coordination, and environmental and social benefits. Addressing these challenges and leveraging these implications can help accelerate the transition to a low-carbon and sustainable future for the manufacture of basic metals sector.