Toward a Carbon-Free Cold forming or folding: Exploring Decarbonization Strategies
This article explores decarbonization strategies for cold forming and folding processes, aiming to reduce carbon emissions and promote sustainable manufacturing practices.
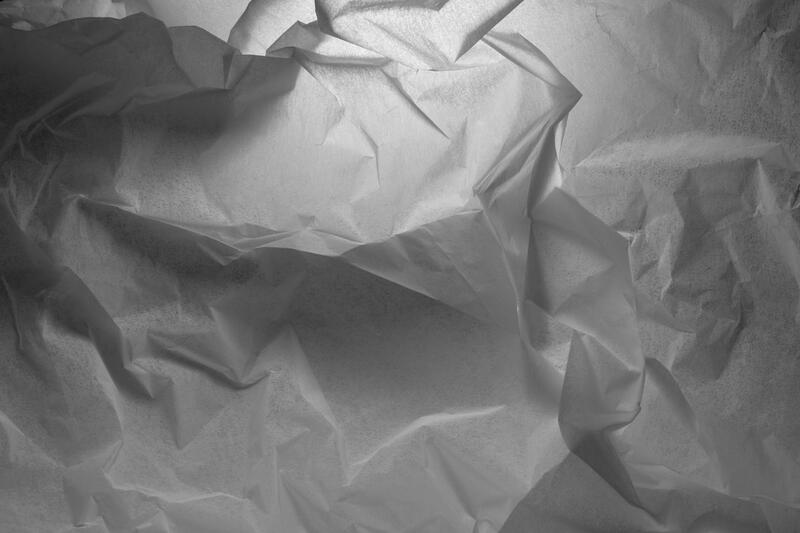
Introduction
The global community is facing an urgent need to reduce greenhouse gas (GHG) emissions to mitigate climate change impacts. Decarbonisation, which refers to the reduction or elimination of carbon dioxide (CO2) emissions, is a critical strategy to achieve this goal. The cold forming or folding sector, which encompasses various industries that produce metal products through plastic deformation at room temperature, is a significant contributor to carbon emissions. This article discusses the importance of decarbonisation in the cold forming or folding sector, the main sources of carbon emissions, strategies to reduce emissions, challenges facing decarbonisation, and the implications of decarbonisation for the sector.
What is Decarbonisation in the Cold Forming or Folding Sector and Why is it Important?
Decarbonisation in the cold forming or folding sector involves reducing carbon emissions associated with the production, transportation, and use of metal products. The sector is a significant contributor to carbon emissions due to the energy-intensive nature of metal production and the use of fossil fuels in transportation. According to the International Energy Agency (IEA), the industrial sector, which includes the cold forming or folding sector, accounts for approximately 37% of global energy-related CO2 emissions (IEA, 2020). Therefore, decarbonisation in the sector is crucial to achieving global climate goals, such as limiting global warming to below 2°C above pre-industrial levels.
The cold forming or folding sector is essential for various industries, such as automotive, aerospace, construction, and consumer goods. Therefore, decarbonisation in the sector can also contribute to sustainable development by promoting resource efficiency, reducing waste, and improving product quality and performance. Furthermore, decarbonisation can create new business opportunities, such as the development of low-carbon technologies, and enhance the competitiveness of the sector in a carbon-constrained world.
What are the Main Sources of Carbon Emissions in the Cold Forming or Folding Sector?
The cold forming or folding sector generates carbon emissions from various sources, including:
- Energy consumption: The production of metal products requires significant amounts of energy, which are often derived from fossil fuels such as coal, oil, and gas. The combustion of these fuels releases CO2 into the atmosphere.
- Transportation: The cold forming or folding sector involves the transportation of raw materials, semi-finished products, and finished products. The use of fossil fuel-powered vehicles, such as trucks, ships, and planes, generates carbon emissions.
- Process emissions: The production of metal products involves various processes that generate CO2 emissions, such as the use of carbon-based reducing agents in iron and steel production and the release of CO2 from limestone during cement production.
- Waste disposal: The cold forming or folding sector generates waste, such as scrap metal and packaging materials, which can emit CO2 during disposal.
How Can We Reduce Carbon Emissions in the Cold Forming or Folding Sector?
To reduce carbon emissions in the cold forming or folding sector, various strategies can be adopted, including:
- Energy efficiency: Improving energy efficiency in the production process can reduce energy consumption and, consequently, carbon emissions. This can be achieved through the use of energy-efficient equipment, process optimization, and waste heat recovery.
- Renewable energy: The use of renewable energy sources, such as solar, wind, and hydropower, can reduce reliance on fossil fuels and, therefore, carbon emissions. Renewable energy can be integrated into the production process through on-site generation or purchasing renewable energy certificates.
- Low-carbon materials: The use of low-carbon materials, such as recycled metal and bio-based materials, can reduce the carbon footprint of metal products.
- Circular economy: The adoption of circular economy principles, such as product design for recyclability and closed-loop material flows, can reduce waste and emissions associated with the disposal of metal products.
- Carbon capture, utilization, and storage (CCUS): CCUS technologies can capture CO2 emissions from industrial processes and either store them underground or use them for other purposes, such as enhanced oil recovery or the production of chemicals.
What are the Challenges Facing Decarbonisation in the Cold Forming or Folding Sector?
Decarbonisation in the cold forming or folding sector faces several challenges, including:
- Cost: The adoption of low-carbon technologies and materials can be expensive, and the cost may be passed on to customers, making the products less competitive.
- Technical feasibility: Some low-carbon technologies, such as CCUS, are still in the development stage and may not be technically feasible or cost-effective for some industries.
- Supply chain complexity: The cold forming or folding sector involves various stakeholders, including raw material suppliers, manufacturers, distributors, and end-users. Coordinating decarbonisation efforts across the supply chain can be challenging.
- Regulatory uncertainty: The lack of consistent and predictable policies and regulations can hinder investment in low-carbon technologies and materials.
- Consumer behavior: The demand for metal products is driven by consumer behavior, which may not prioritize sustainability. Therefore, promoting sustainable consumption and behavior change is essential for decarbonisation in the sector.
What are the Implications of Decarbonisation for the Cold Forming or Folding Sector?
Decarbonisation in the cold forming or folding sector has several implications, including:
- Innovation: Decarbonisation can drive innovation in the sector, leading to the development of new low-carbon technologies, materials, and business models.
- Competitiveness: Decarbonisation can enhance the competitiveness of the sector by reducing costs, improving product quality, and meeting customer demand for sustainable products.
- Collaboration: Decarbonisation requires collaboration across the supply chain, leading to closer relationships between stakeholders and the development of new partnerships.
- Regulatory compliance: Decarbonisation can help the sector comply with existing and future regulations aimed at reducing carbon emissions.
- Reputation: Decarbonisation can enhance the reputation of the sector by demonstrating its commitment to sustainability and social responsibility.
Conclusion
Decarbonisation in the cold forming or folding sector is essential to mitigate climate change impacts, promote sustainable development, and enhance the competitiveness of the sector. The sector generates carbon emissions from various sources, including energy consumption, transportation, process emissions, and waste disposal. To reduce emissions, various strategies can be adopted, such as energy efficiency, renewable energy, low-carbon materials, circular economy, and CCUS. However, decarbonisation faces several challenges, such as cost, technical feasibility, supply chain complexity, regulatory uncertainty, and consumer behavior. Decarbonisation has several implications, such as innovation, competitiveness, collaboration, regulatory compliance, and reputation. Therefore, the cold forming or folding sector must prioritize decarbonisation efforts to achieve a sustainable and low-carbon future.