Strategies for Achieving Decarbonization in Casting of iron: A Deep Dive
This article explores various methods for reducing carbon emissions in the casting of iron, including the use of renewable energy sources and process optimization.
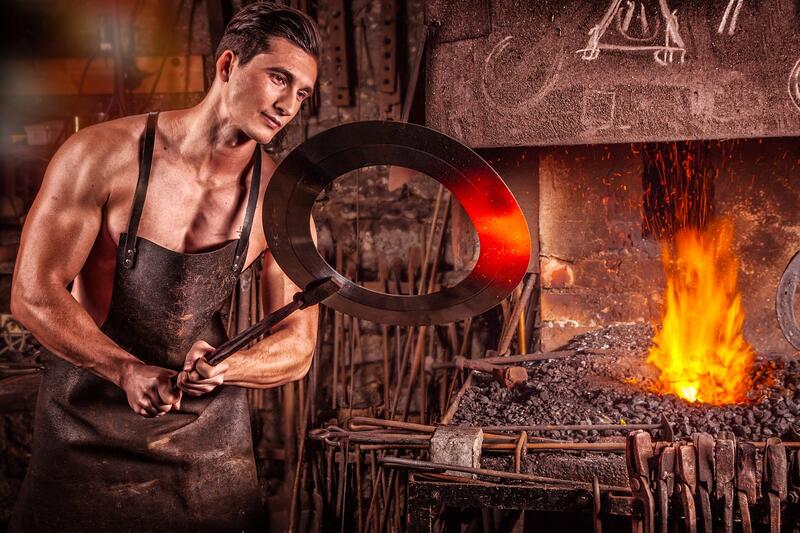
The casting of iron is a critical component of the manufacturing industry, with applications in construction, automotive, and aerospace sectors. However, the process of casting iron is energy-intensive and emits a significant amount of carbon dioxide (CO2) into the atmosphere. As the world grapples with the challenge of climate change, decarbonisation of the casting of iron sector has become an urgent priority. This article explores the concept of decarbonisation in the casting of iron sector, its importance, sources of carbon emissions, strategies for reducing carbon emissions, challenges, and implications for the sector.
What is Decarbonisation in the Casting of Iron Sector and Why is it Important?
Decarbonisation refers to the reduction or elimination of carbon emissions from industrial processes and energy systems. In the casting of iron sector, decarbonisation involves the adoption of technologies and practices that reduce the carbon footprint of the process. The importance of decarbonisation in the casting of iron sector cannot be overstated. The sector is a significant contributor to global carbon emissions, accounting for approximately 7% of global CO2 emissions. The casting of iron process involves the use of fossil fuels, such as coal and natural gas, which emit CO2 when burned. Additionally, the process of producing iron involves the use of coke, a carbon-rich material that emits CO2 during the production process. Decarbonisation is, therefore, crucial in reducing the sector's carbon footprint and mitigating climate change.
What are the Main Sources of Carbon Emissions in the Casting of Iron Sector?
The casting of iron process involves several stages, each of which contributes to carbon emissions. The main sources of carbon emissions in the casting of iron sector include:
- Energy consumption: The casting of iron process requires significant amounts of energy, which is usually generated by burning fossil fuels. This results in the emission of CO2 into the atmosphere.
- Raw materials: The production of iron involves the use of coke, a carbon-rich material that emits CO2 during the production process.
- Transportation: The transportation of raw materials and finished products also contributes to carbon emissions.
- Waste disposal: The disposal of waste products, such as slag, also contributes to carbon emissions.
How Can We Reduce Carbon Emissions in the Casting of Iron Sector?
Reducing carbon emissions in the casting of iron sector requires a multifaceted approach that involves the adoption of various technologies and practices. Some of the strategies for reducing carbon emissions in the casting of iron sector include:
- Use of renewable energy: The adoption of renewable energy sources, such as solar and wind power, can significantly reduce the sector's carbon footprint. Renewable energy can be used to power the casting process, reducing the need for fossil fuels.
- Carbon capture and storage (CCS): CCS involves capturing CO2 emissions from the casting process and storing them underground. This technology can significantly reduce the sector's carbon footprint.
- Energy efficiency: Improving the energy efficiency of the casting process can reduce the amount of energy required, thereby reducing carbon emissions.
- Use of alternative materials: The use of alternative materials, such as scrap metal, can reduce the need for coke, thereby reducing carbon emissions.
- Recycling: Recycling scrap metal can reduce the need for new iron production, thereby reducing carbon emissions.
What are the Challenges Facing Decarbonisation in the Casting of Iron Sector?
The decarbonisation of the casting of iron sector is not without its challenges. Some of the challenges facing decarbonisation in the sector include:
- Cost: The adoption of new technologies and practices can be expensive, making it challenging for some companies to invest in decarbonisation.
- Technical feasibility: Some of the decarbonisation strategies, such as CCS, are still in the early stages of development and may not be technically feasible for all companies.
- Regulatory barriers: Some countries may not have regulations in place to support decarbonisation, making it difficult for companies to invest in the process.
- Lack of public awareness: The public may not be aware of the importance of decarbonisation in the casting of iron sector, making it challenging to garner support for the process.
What are the Implications of Decarbonisation for the Casting of Iron Sector?
The implications of decarbonisation for the casting of iron sector are significant. Decarbonisation can lead to a more sustainable and environmentally friendly sector. The adoption of renewable energy sources and the reduction of carbon emissions can help mitigate climate change and reduce the sector's impact on the environment. Additionally, decarbonisation can lead to new business opportunities, such as the development of new technologies and practices. However, the process of decarbonisation may also lead to job losses in the short term as companies transition to new technologies and practices. Therefore, it is crucial to ensure that the process of decarbonisation is managed in a way that is socially and economically sustainable.
Conclusion
The casting of iron sector is a significant contributor to global carbon emissions, making decarbonisation a crucial priority. The adoption of new technologies and practices, such as renewable energy sources, CCS, and energy efficiency, can significantly reduce the sector's carbon footprint. However, the process of decarbonisation is not without its challenges, including cost, technical feasibility, and regulatory barriers. Despite these challenges, the decarbonisation of the casting of iron sector is essential in mitigating climate change and creating a more sustainable and environmentally friendly sector.